Carbon Fiber: Material Properties, Manufacturing, and Performance
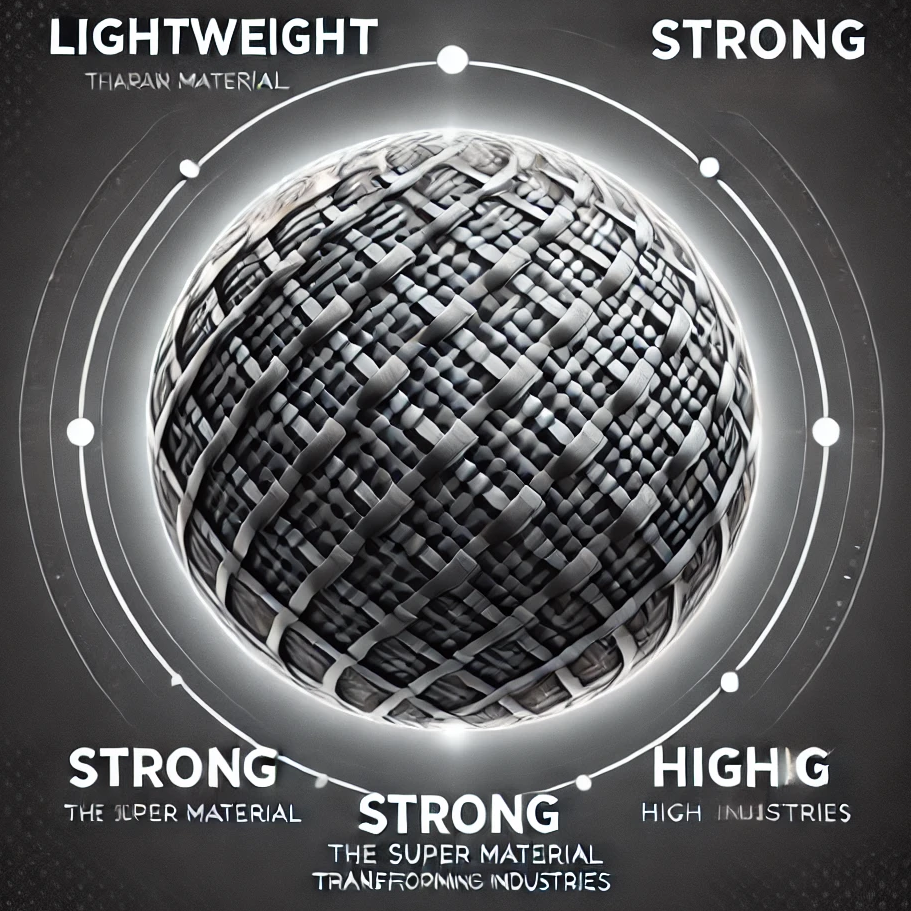
Podcast
Carbon fiber is one of the most versatile and advanced materials available today, offering a combination of lightweight, high strength, and excellent performance in various applications. From aerospace and automotive industries to sporting equipment and energy, carbon fiber has reshaped what we can accomplish in engineering and design. In this blog, we will conduct an in-depth quantitative analysis of carbon fiber’s properties, including its material, mechanical, thermal, electrical, and manufacturing aspects. The comparison will include data tables and visuals to illustrate the unique advantages of carbon fiber over other materials like steel and aluminum.
Material Properties
Carbon fibers are primarily made of thin, crystalline filaments of carbon atoms arranged in a well-aligned structure. This alignment gives carbon fiber its superior properties. The following table summarizes the key material properties of carbon fiber compared to steel and aluminum:
Property | Carbon Fiber | Steel | Aluminum |
---|---|---|---|
Density (g/cm³) | 1.75 | 7.85 | 2.70 |
Young's Modulus (GPa) | 230 | 210 | 70 |
Tensile Strength (MPa) | 4000 | 400 - 1500 | 200 - 550 |
Poisson's Ratio | 0.2 | 0.27 - 0.3 | 0.33 |
Carbon fiber's density is significantly lower than that of steel and aluminum, making it an ideal choice for applications requiring high strength-to-weight ratios. The tensile strength and Young's modulus are particularly impressive, making carbon fiber not only lighter but also stronger than most metals.
Mechanical Properties
The mechanical properties of carbon fiber are exceptional, particularly in its ability to bear loads. The following comparison chart shows the strength-to-weight ratio of carbon fiber versus other materials:
Material | Strength-to-Weight Ratio (kN·m/kg) |
---|---|
Carbon Fiber | 245 |
Steel | 50 |
Aluminum | 90 |
Thermal Properties
Thermal properties play a crucial role in selecting materials for specific applications, especially where temperature resistance is key.
Property | Carbon Fiber | Steel | Aluminum |
---|---|---|---|
Thermal Conductivity (W/mK) | 6 - 20 | 50 | 235 |
Coefficient of Expansion (µm/m°C) | 0 - 1 | 11.7 | 23.1 |
Max Working Temp (°C) | 300 - 500 | 1370 | 660 |
Carbon fiber has a low thermal conductivity, which is advantageous in situations where heat insulation is required. Moreover, its coefficient of thermal expansion is nearly zero, meaning it remains stable under varying temperatures, unlike metals such as steel and aluminum, which expand or contract more significantly.
Manufacturing Process
Manufacturing carbon fiber involves several stages, including the production of precursor fibers (usually polyacrylonitrile, or PAN), oxidation, carbonization, and surface treatment. Each step impacts the quality and properties of the final product.
- Precursor Production: Typically made from PAN or rayon, accounting for about 90% of carbon fiber production.
- Oxidation: The precursor fibers are stabilized through heating in an oxygen-rich environment.
- Carbonization: Heated to extremely high temperatures (up to 2000°C) in an inert atmosphere to remove non-carbon elements.
- Surface Treatment and Sizing: Improves bonding with resins for composite production.
Manufacturing Cost Comparison:
Compared to metals, carbon fiber is costlier to produce, which has historically limited its adoption to high-performance industries. However, advancements in manufacturing processes and increasing demand have led to a gradual decline in costs, enabling its use in a broader range of applications.
Electrical Properties
Carbon fiber has unique electrical properties, making it useful for specific niche applications, particularly in aerospace and electronic industries.
Property | Carbon Fiber | Steel | Aluminum |
---|---|---|---|
Electrical Conductivity (S/m) | 10^4 - 10^5 | 10^7 | 3.8x10^7 |
Resistivity (Ω·m) | 1.5x10^-5 | 1.6x10^-7 | 2.8x10^-8 |
While carbon fiber is not as conductive as metals like aluminum or steel, it still offers conductivity useful for EMI shielding in electronic applications. The relatively higher resistivity also makes it a suitable candidate for certain specialized electrical applications, such as creating resistance heating elements.
Application Areas
The combination of unique material, mechanical, thermal, and electrical properties makes carbon fiber an attractive choice for many industries:
- Aerospace and Aviation: High strength and low weight help improve fuel efficiency and overall performance.
- Automotive: Used in high-performance cars to reduce weight and enhance speed and fuel efficiency.
- Sports Equipment: Rackets, bicycles, and golf clubs often use carbon fiber for improved strength and reduced weight.
- Wind Turbines: Carbon fiber-reinforced blades improve efficiency due to their lightweight and high strength.
Conclusion
Carbon fiber is a high-performance material that offers an outstanding balance between weight, strength, and thermal stability, making it suitable for applications where performance is critical. However, its higher cost and manufacturing complexity have somewhat limited its widespread adoption. With continued advancements in production technology and declining costs, carbon fiber has a promising future across multiple industries, from automotive to renewable energy.
Future Outlook
As we look ahead, advancements in carbon fiber manufacturing, such as recycling methods and lower-cost precursors, are expected to reduce overall production costs. Combined with increasing demand for lightweight, high-strength materials, we can anticipate even broader adoption of carbon fiber in various industries.